Delamination of laminated glass: its causes and how to prevent it
Share this blog:
Glass delamination is the result of poor processing and installation. Find out how we can help you avoid it.
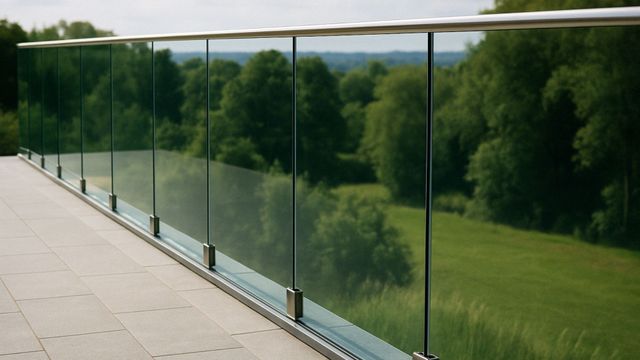
Laminated glass is built to last. But that doesn't mean it lasts forever. Sometimes, homeowners and business owners will spot a defect in their laminated glass: a stain caused by the wearing away of the glass's plastic interlayer.
Este es un defecto específico del vidrio laminado y su método de fabricación. La mayoría de los tipos de vidrio constan de una sola capa. El vidrio laminado, en cambio, consta de dos (o más) láminas de vidrio que encierran una capa intermedia de plástico.
Este método de construcción confiere al vidrio laminado su extraordinaria robustez. También es la razón por la que se rompe de esa manera. En lugar de romperse, la superficie impactada se agrieta, pero permanece en su lugar. Esto lo convierte en un tipo de vidrio de seguridad, lo que significa que puede utilizarse en aplicaciones donde la seguridad es primordial.
Sin embargo, ser robusto no significa ser indestructible. La delaminación se produce cuando la unión adhesiva entre el vidrio y la capa intermedia se reduce o desaparece por completo. Esto ocurre con mayor frecuencia en láminas de vidrio laminado con una capa intermedia de PVB (un tipo particular de plástico).
Entonces, ¿cuáles son las causas de la delaminación y cómo se puede evitar? Se debe principalmente a una instalación inadecuada. Sin embargo, también puede deberse a productos de mala calidad. Por eso es tan importante trabajar con un procesador de vidrio de confianza.
¿Cuáles son las causas de la delaminación?
Hay cuatro causas principales de delaminación: dos se deben a una instalación deficiente y dos a un procesamiento deficiente.
1. Exceso de humedad
La primera y más común causa de delaminación es la exposición del vidrio laminado a un exceso de humedad. El PVB (el material utilizado para muchas láminas intermedias) es higroscópico. Esto significa que absorbe y retiene la humedad.
Si los paneles de vidrio están expuestos a una humedad excesiva, la unión puede reducirse y puede producirse delaminación.
Esto suele ser consecuencia directa de una mala instalación. El borde de una lámina intermedia debería "respirar". Si no lo hace, es muy probable que se produzca delaminación.
2. Silicona incompatible
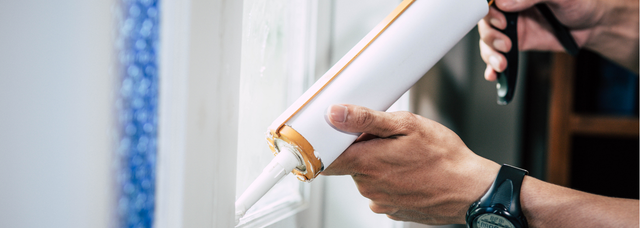
En segundo lugar, está la cuestión de la silicona estructural. Esta debe ser compatible con la capa intermedia. Si se recorta esta compatibilidad, podría producirse delaminación.
3. Mal procesamiento del vidrio.
En tercer lugar, existe un procesamiento deficiente. Un procesador de vidrio utiliza limpiadores e imprimaciones para preparar el vidrio antes de unirlo con silicona estructural. Si estos no se eliminan por completo, pueden empezar a desgastar la capa adhesiva y contribuir a la delaminación.
4. Distorsión de onda rodante
Finally, there's something called
"roller wave distortion". This isn't something that glass processors can eliminate entirely – but a good processor will make sure it's kept to a minimum.
Se produce cuando los rodillos utilizados en el proceso de fabricación distorsionan el vidrio de forma desigual. Estas distorsiones pueden ejercer tensión sobre la capa intermedia, especialmente en los bordes, donde es más probable que se produzca delaminación.
¿Qué podemos aprender de esto? Quizás la lección clave sea que debes elegir con cuidado a tus procesadores e instaladores. De lo contrario, corres el riesgo de decepcionarte.
¿Qué capas intermedias son más susceptibles?
Los distintos productos de vidrio laminado utilizan distintas capas intermedias de plástico. En ToughGlaze, por ejemplo, utilizamos con mayor frecuencia PVB (butiral de polivinilo). Este es el tipo de capa intermedia más común y también el más susceptible a la delaminación.
Sin embargo, esto solo supone un problema si se adquiere vidrio laminado de un fabricante deficiente o si se recibe un vidrio laminado de buena calidad mal instalado. Sin embargo, en buenas manos, el PVB es la capa intermedia más común por algo.
Las capas intermedias de resina también son susceptibles a la delaminación y pueden deteriorarse bajo la radiación UV.
Los poliuretanos e ionoplastos, como Sentry Glass y EVA (etileno-acetato de vinilo), son menos susceptibles a la delaminación que el PVB. Sin embargo, los poliuretanos pueden expandirse con el calor y el EVA presenta un rendimiento inferior al del PVB bajo cargas explosivas.
Why does it matter?
La razón obvia por la que la delaminación es importante es que se ve fea. Claro que, a veces, la experiencia puede variar: a algunas personas les gusta un aspecto de hogar. Pero para la mayoría de los propietarios de viviendas y negocios, la delaminación es algo que debe evitarse por razones puramente estéticas.
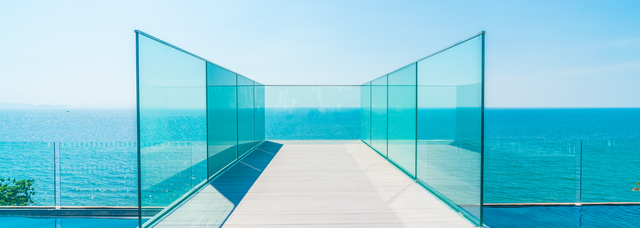
Sin embargo, existe una razón aún más importante para garantizar la instalación de vidrio laminado de alta calidad. Esto se debe a que la delaminación debilita el vidrio. Dado que uno de los principales objetivos del vidrio laminado es brindar mayor seguridad, esto es algo que debe evitarse siempre que sea posible.
The UK's
National Protective Security Authority (NPSA), for instance, conducted an experiment where it subjected four laminated windows to a TNT-strength blast load. Three of the panes had different depths of delamination, while the fourth was as good as new.
La NPSA descubrió que "el vidrio se saldrá del marco y se desplazará hacia el interior del edificio (cubículo de prueba) cuando haya 12-15 mm o más de delaminación del borde lineal en los cuatro lados".
En otras palabras, la delaminación puede comprometer la robustez del vidrio laminado y hacerlo vulnerable a impactos de explosión. Solo por esta razón, vale la pena invertir en vidrio laminado de alta calidad y trabajar con instaladores de alta calidad.
¿Cómo se puede prevenir la delaminación?
Lo mejor es trabajar con un procesador de vidrio que tenga un alto nivel de control de calidad durante el proceso de fabricación. Busque la certificación ISO 9001:2015, el estándar internacional de oro para el aseguramiento de la calidad industrial.
A continuación, debería trabajar con un instalador de confianza. Esto garantizará que la silicona estructural y las juntas sean compatibles, que los bordes estén ventilados y que la lámina intermedia no quede comprimida por el marco ni los herrajes.
Finalmente, puede mencionar la delaminación al especificar el vidrio. La NPSA recomienda estipular niveles aceptables de delaminación e incluso ofrece una plantilla que puede usar al comunicarse con un procesador de vidrio.
¿Cuál es la esperanza de vida del vidrio laminado?
Con un mantenimiento adecuado, el vidrio laminado puede durar entre 25 y 50 años. Sin embargo, es menos probable que tenga una vida útil tan larga si trabaja con un instalador o procesador deficiente.
So, if you're in the market for high-quality
laminated glass products, don't hesitate to
contact ToughGlaze. We'll fix you up with best-in-class materials that are built to last, not to delaminate.